Instrument
design is a constant challenge of pushing the envelope to produce
a more efficient guitar. I believe that while actual body shapes
and designs are somewhat important the accuracy and quality of
the construction is perhaps even more critical. So with that in
mind I'll offer a little insight into some of my designs, construction
techniques and various shop jigs & tooling.
Design
Concepts
An
individual builder has much greater freedom to experiment with
designs than a factory might. Factories must concentrate on production
methods and achieving consistent results from a huge range of
type and quality of materials. Additionally, most factory guitars
are also overbuilt in the interest of minimizing warranty claims.
In fact, I believe most guitars are overbuilt to some degree....the
trick is finding the right balance between durability and sound
production. You really can have both.
So
although I use a traditional X-brace pattern on my soundboards
I can brace them fairly lightly with no loss of durability mainly
due to three key elements that strengthen the upper bout area:
1.) The Bolt-on Neck Joint, 2.) Adding a "paddle" to
support the fingerboard, and 3.) Supporting the soundhole area
under the rosette. These three elements result in gains in volume
and sustain as well as more stable necks and action height. In
more detail...
The
Bolt-on Neck Joint
Traditional
dovetail neck joints are a perfectly adequate way to attach a
neck. However, I find that employing a full 3/4" slip-fit
mortise and tenon joint offers significant advantages. First,
the bolt-on design enhances stability and vibration transference
thru the use two mechanical fasteners that pull the heel snugly
into the neckblock and against the guitar sides. Second, this
method improves the accuracy of manufacture. Neck angles can be
precisely set (or re-set) without disturbing the strength of the
joint since no glue surfaces are affected by changes. Third, the
neck is easily removed by loosening the fasteners and lifting
the fingerboard from the top in the traditional way. This can
be accomplished in less than fifteen minutes with no worry of
damage from "steaming" the joint apart.
Fingerboard
Paddle
Shown
here is the neckblock with a birch ply paddle. The ply material
is used because of its inherent strength to weight ratio. It is
stronger and more stable than either mahogany or spruce, both
of which I have tested. The paddle provides complete support for
the fingerboard area and will ultimately provide a platform for
small bolts which replace the function of glue in holding the
fingerboard snug onto the soundboard. Also visible on the neckblock
is one of the countersunk bolt holes used for neck attachment.
As a final touch a matching mahogany filler strip is fitted into
the channel to hide the bolt heads.
Soundhole
Support
A
cross-grain patch of matching spruce is used to support the underside
of the rosette area and prevent distortion of this weakened area.
Not shown in this picture are the additional two braces added
on either side of the patch or the X-brace and upper transverse
braces. Classical makers use a similar support patch as a matter
of tradition.
Pinless
Bridge
The
new Pin-less bridge is now available as a "standard"
feature if requested. Designed with CAD CAM technology, the new
bridge is machined on a Fadal CNC machine for accuracy.
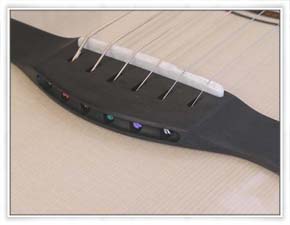
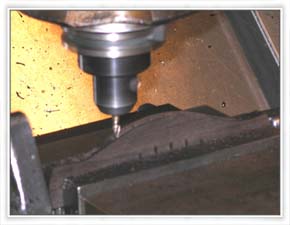